Induction Brazing’s Applications across Industries
Brazing is a metal-joining process. It employs a filler metal and often an anti-oxidizing flux. The aim is to connect two metal pieces without melting the base materials. Instead, heat induction melts the filler. Through capillary action, the melted filler then gets drawn into the base materials.
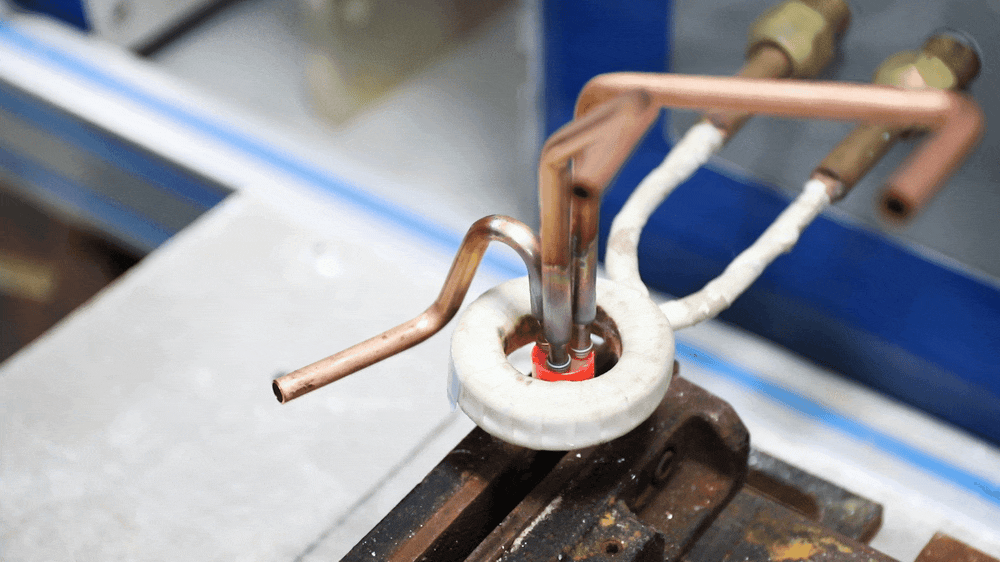
Comparing Soft Soldering and Brazing
Generally, soft soldering (< 450 °C) and brazing (>450 °C) are different. Brazing is adopted when the goal is to achieve a mechanically strong connection. On the other hand, if only tightness and electrical conductivity are required, soft soldering is the choice. Solders are often alloys based on silver or copper.
Advantages of Induction Brazing
Compared to other soldering methods, the advantages are as follows: reproducible quality of soldered joints, capable of being automated, fast and precise. Moreover, it doesn’t affect the surrounding areas, it’s clean, 省エネ, and emits no CO2 when using green electricity.
Induction brazing is a brazing method in which the workpiece is heated by the resistance heat of the induced current generated in the alternating magnetic field of alternating current. Since the heat is generated by the workpiece itself, it heats up rapidly, and the oxidation on the workpiece surface is less than that in furnace brazing. Moreover, it can prevent the growth of the grain of the base materials and the development of recrystallization. In addition, localized heating of the workpiece can also be achieved.
The alternating current can be divided into power frequency, medium frequency and high frequency. Power frequency is seldom used for brazing, while high frequency and medium frequency are commonly used for induction brazing.
Various brazing filler metals can be used in induction brazing. Due to the very high heating speed of induction brazing, both the brazing filler metal and the flux are placed in advance during assembly. Induction brazing can be carried out not only in the air but also in a vacuum or a protective atmosphere. In such cases, both the workpiece and the induction coil can be placed into the container at the same time, or the container with the workpiece can be placed inside the induction coil, and then the container is evacuated or filled with protective gas.
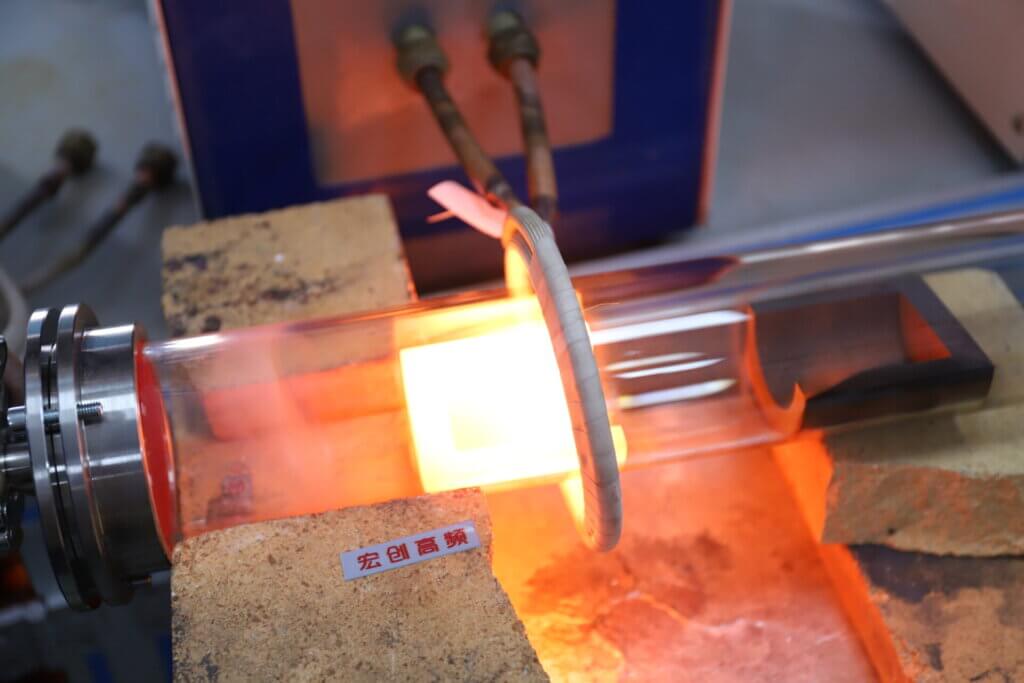
With the improvement and perfection of equipment precision and control methods, induction brazing has been widely applied to the brazing of aluminum and aluminum alloys at present. In addition, since induction brazing can easily achieve automation and rapid local heating, it is also a very effective process for the mass production of workpieces.
Application Industries:
1. Automobile air conditioners
Heat exchangers widely used in automobiles (including components such as automobile air conditioner condensers, evaporators, radiator tanks, and oil coolers) have seen the emergence of aluminum heat exchangers since the 1970s. Compared with traditional all-copper heat exchangers, aluminum heat exchangers have the characteristics of high heat exchange efficiency, light weight, cost savings, and reduced fuel consumption of automobiles.
The components of automotive air conditioners suitable for brazing include condensers, receivers, distributors, piping parts, and various pressure plate joints.
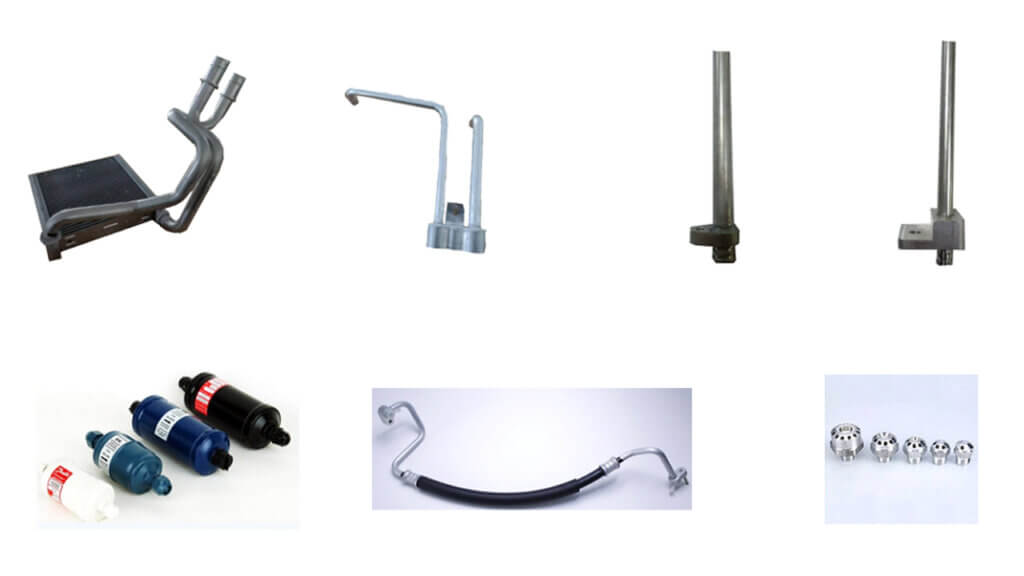
2. Liquid cooling pipes for new energy vehicles.
To meet the power supply requirements of high-power electrical appliances, multiple batteries are usually connected in series or in parallel to form a battery pack for power supply. When multiple batteries supply power, a large amount of heat will inevitably be generated. If an effective cooling system is not adopted to cool them down, it will not only seriously affect the service life of the batteries but also pose a significant safety hazard. The cooling system with flat tubes and manifolds has been widely used in the new energy electric vehicle industry due to its advantages such as light weight and good heat dissipation performance.
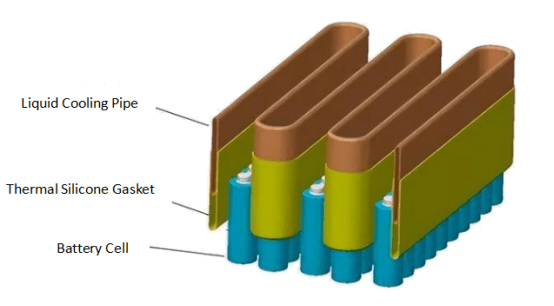
3.自転車産業
Aluminum alloy frames have the advantages of light weight, good elasticity, and good resistance to moisture oxidation. It is the mainstream material for bicycle frames at present. In the manufacturing process of aluminum alloy bicycles, the brazing technique plays a crucial role in many key parts.
The components of bicycles suitable for brazing include the brake posts, cable guides and other accessories on the frame, as well as the brazing of tubes and accessories such as the head tube, front fork, rear fork and rear seat.
4. HVAC Industry
HVAC manufacturers used to depend largely on flame brazing, yet recently the industry is turning to induction brazing. The latter’s equipment offers controllable heat, guaranteeing high-quality and consistent brazed joints, thus becoming the top choice for brazing operations. Induction brazing suits high-volume, repetitive joining tasks well. Our equipment provides instant, stable heating with precise control, without an open flame, enhancing safety and lessening environmental impact.
This is Air Conditioning Capillary Tube used in the refrigeration and HVAC industries.
Hongchuang has long been supplying induction brazing solutions to leading manufacturers in these sectors. Our team is experienced in devising customized systems to fit into current assembly lines. Depending on specific process needs, we provide manual, semi-automatic or fully automated robotic systems.